In the application process of the feed pellet machine, maintenance work should be carried out for the pellet machine regularly to make the pellet feed machine work normally. We also need to regularly maintain and maintain the power unit of the pellet machine to prevent machine failures and ensure the smooth operation of the equipment. So how should the feed pellet machine be maintained?
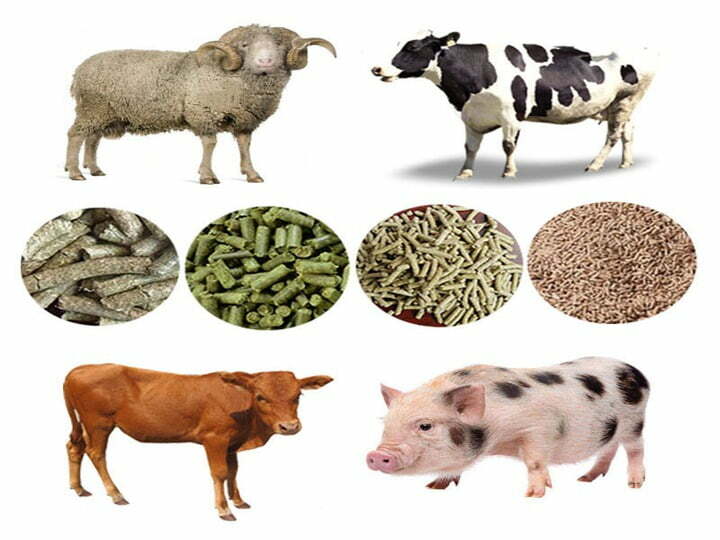
Steps for maintaining of feed pellet machine
- Before using the poultry feed pellet machine, first check whether the screws of each part of the machine are tight.
- Before starting the machine, loosen the two adjusting screws on both ends of the pressure roller, then start the motor, and observe whether the transmission of the machine is the same as the mark.
- Run-in of the new grinding disc: The grinding disc of the pellet machine should be run-in before being used for the first time. Running-in method: Take 5 kg of raw materials and 1 kg of fine sand and mix well, then add 1 kg of waste engine oil and mix thoroughly. Start the machine, put in the evenly mixed raw materials, adjust the pressure roller bolts with a wrench, and wait until the materials are discharged normally. (Note: the adjustment gap should not be too small, too small will damage the pressure roller and grinding plate) Keep the machine running for 1 hour before adding conventional raw materials for production. If the pellets cannot be discharged normally after adding the raw materials, the pressure roller bolts should be slightly loosened until the material is discharged normally. When the operator finishes the day’s granulation work, after the raw material is pressed, the raw material and 10% waste oil are mixed and added to the machine to fill the mold hole of the grinding disc and ensure that the mold hole is not blocked. In this way, the operator will be ready for the next normal production and will save a lot of time when starting the equipment next time.
- Raw material requirements: The moisture content of the material should be adjusted to 14%-18%. Too high or too low moisture content will affect the output and quality of feed pellets; at the same time, the raw materials should be mixed uniformly and ensure the same moisture content.
- The feed pellet machine should stop feeding before shutting down. After the material in the silo is processed, add oily material and press it into the template hole to keep the hole smooth so that it will not be blocked next time.
- Under normal production conditions, the pressure roller bearing must be cleaned with gasoline or diesel oil once every five days, and high-speed lubricating oil must be injected at the same time.
- Adjustment of the gap between the grinding plate and the pressure roller of the pellet machine: The gap between the pressure roller and the die plate has a greater impact on the granulation quality, and the general gap should be between 0.05 and 0.3 mm. When the gap is greater than 0.3 mm, the material layer is too thick and uneven distribution will reduce the pelleting output. When the gap is less than 0.05 mm, the machine will be severely worn.
- Selection of grinding disc hole depth and aperture (compression ratio): The grinding disc with small hole depth and aperture ratio has high granulation output but low hardness. On the contrary, the yield is low and the hardness is high. Therefore, users should choose different grinding discs according to their own needs. If necessary, you can mail raw materials to us, and we can customize suitable grinding discs for you.
- Adjustment of the length of feed pellets: Adjust the length of pellets by adjusting the height of the cutter set above the outlet of the feed pellet machine.
- How to replace the grinding disc of the feed pellet machine: Use a screwdriver to flatten one of the teeth of the stop washer inserted into the nut notch on the main shaft, use a hook wrench (spare part) to unscrew the nut, take out the stop washer and flat washer, and then use Take out the mold from the mold screwdriver (spare part). After replacing the new mold plate, it is necessary to re-run-in according to the aforementioned method.
- Processing method of processed feed pellets: The processed pellet feed has a relatively high temperature and should be placed in a ventilated place to cool to room temperature before bagging and storage.