The Sawdust Wood Pallet Block Machine can transform waste biomass materials like sawdust and wood shavings into high-density compressed pallet blocks. These blocks are used as footings for wooden pallets and packaging boxes, offering a sustainable alternative to solid wood.
With a capacity ranging from 2 to 6 cubic meters per 24 hours, and block sizes customizable from 75mm to 145mm, the machine meets the demands of both small-scale and industrial pallet production lines.
Its automatic feeding system, precise heating control, and robust hydraulic pressing system ensure consistent quality and high production efficiency, making it a cost-effective solution for recycling wood waste into valuable products.
What is the sawdust wood pallet block?
Sawdust wood pallet blocks serve as essential components of wooden pallets, primarily functioning as their support feet. These blocks, produced by specialized extruder machines, differ significantly from conventional wood blocks that are typically nailed together with wooden boards.
The manufacturing process results in sawdust pallet blocks that are smooth on all sides and possess high strength, enabling them to replace solid wood foot piers effectively.
A key advantage of these wood blocks is that they are fumigation-free, making them ideal for use in export fumigation-free pallets and packing boxes both domestically and internationally.
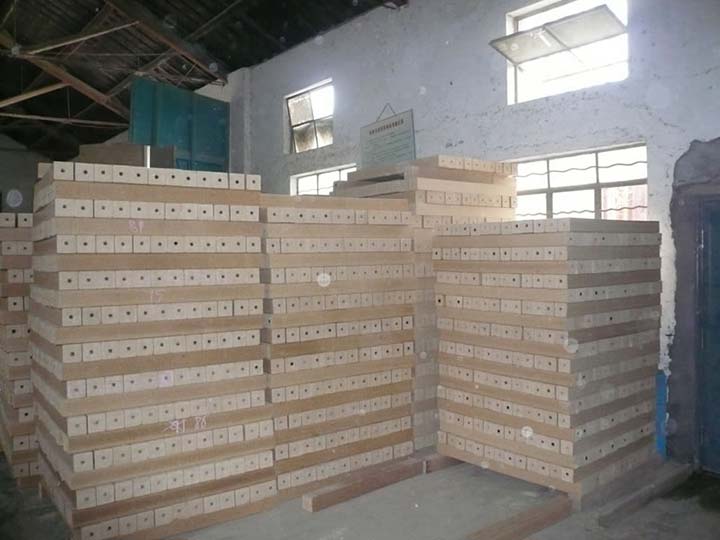
Raw materials for making sawdust wooden blocks
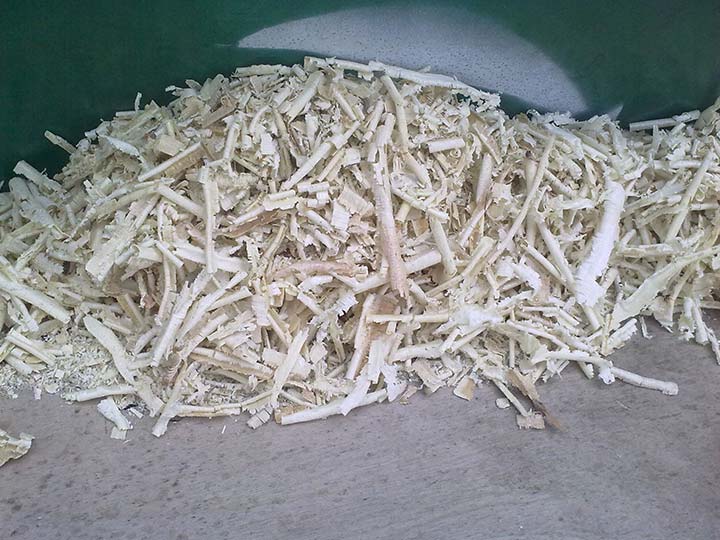
A diverse array of waste biomass materials serves as the raw resources for manufacturing sawdust wooden blocks.
These materials encompass branches, sawdust, wood processing remnants, wood shavings, rice husks, straw, pine, hardwood, logs, among others.
Prior to the production of sawdust pallet blocks, these raw materials must undergo processing through a wood shredder to be transformed into sawdust.
Wood pallet block machine for sale
If you’re in the market for a wood pallet block machine, you’ll find our equipment to be highly efficient and versatile. As the primary device for processing wooden cubes and tiles, it comes equipped with two reverse feed inlets designed for sawdust storage. Additionally, the machine features four outlets dedicated to the extrusion of pallet blocks.
Our sawdust pallet block making machine incorporates electric heating functionality. During the wood block extrusion process, the heating plate remains continuously heated, enabling the lignin in the sawdust to melt and bind together.
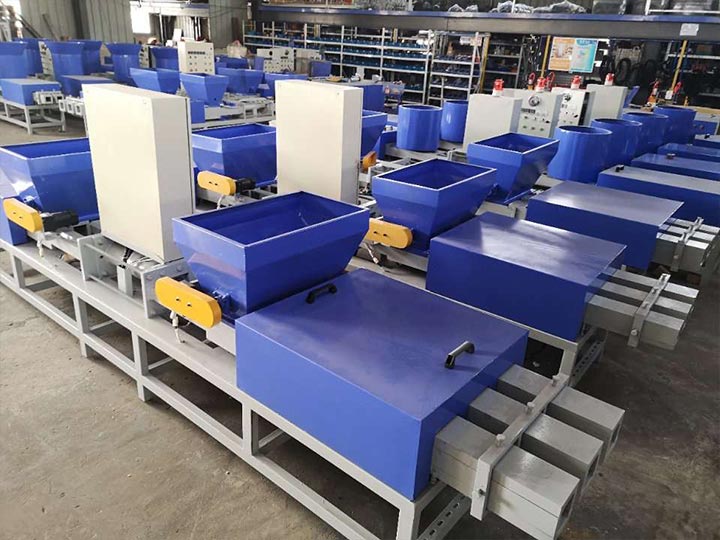
This results in pallet blocks that are more solid and have a higher density. Furthermore, the export mold of the machine can be easily replaced with molds of various sizes, allowing you to produce wooden blocks that meet different specifications.
Whether you’re looking to process wooden cubes for pallets or tiles, our wood pallet block machine offers excellent performance and adaptability. Its advanced features and efficient operation make it an ideal choice for businesses seeking to enhance their wood processing capabilities.
How to make pallet blocks with the wood pallet block machine?
To produce pallet blocks using a wood pallet block machine, start by mixing sawdust with glue, typically urea-formaldehyde resin glue at around 16% concentration.
Use a specialized mixer to combine the sawdust or wood shavings thoroughly. Next, evenly feed the well-mixed raw materials into the machine’s feed port.
The machine’s inner screw and hydraulic system work together to push the material into the heating system of its discharge.
A cutting device installed at the discharge port allows you to cut the extruded wood blocks to a desired length.
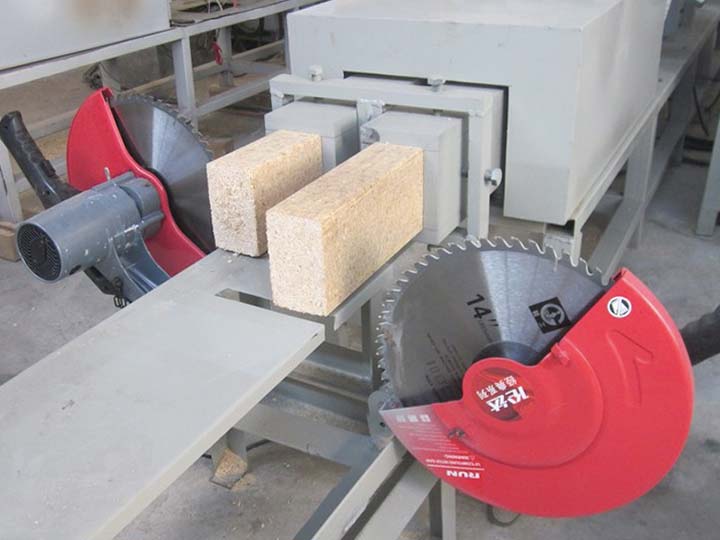
Pallet blocks with holes VS non-holes pallet blocks
Pallet blocks, whether with holes or non-holes, each have their own distinct features and applications. Here’s a detailed comparison between the two:
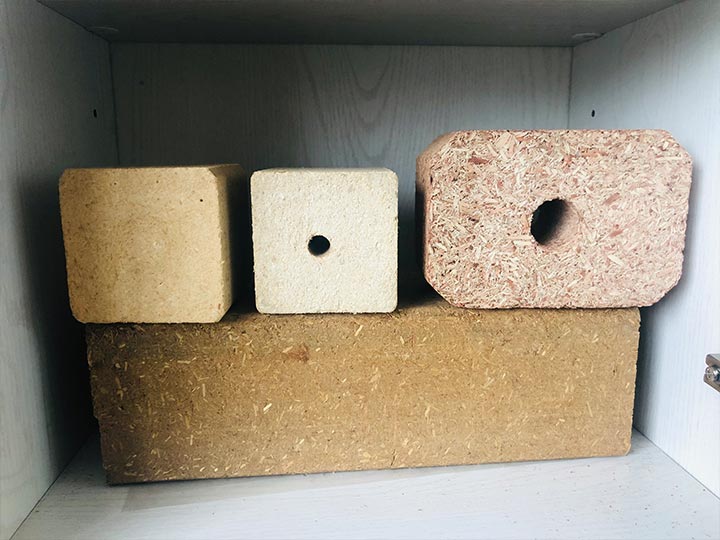
Pallet blocks with holes
During the production of pallet blocks with holes, methanol and water vapor can escape through the central longitudinal hole. This unique design gives the wooden cubes good air permeability, preventing them from expanding due to moisture, which in turn helps to extend their service life.
However, when nailing these blocks, it’s crucial to avoid the small round hole in the middle. Otherwise, there’s a risk of the nail accidentally entering the central hole, potentially compromising the structural integrity of the pallet.
Non-holes pallet blocks
Non-holes pallet blocks, as the name suggests, are completely dense with no holes in the middle. This makes them more convenient for nailing, as there’s no risk of nails accidentally entering a hollow space.
The absence of holes also contributes to a more uniform distribution of stress across the block, enhancing the overall stability and load-bearing capacity of the pallet.
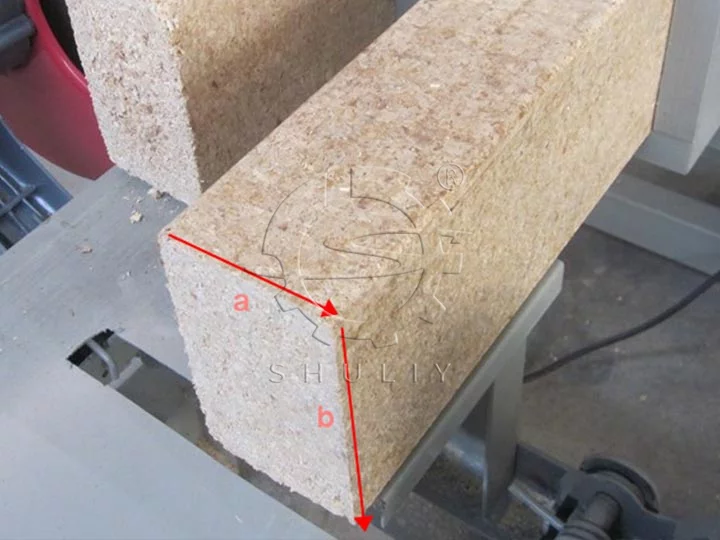
The decision to use pallet blocks with holes or non-holes largely depends on the specific requirements of the user. If air permeability and moisture resistance are priorities, then pallet blocks with holes may be the preferred choice. On the other hand, if ease of nailing and maximum load-bearing capacity are more important, non-holes pallet blocks would be more suitable.
In general, the higher the density of the wood cubes, the better their load-bearing capacity, which is a key factor to consider when selecting pallet blocks for different applications.
Parameters of wood pallet block making machine
Model | Power | Capacity | Dimension | Weight |
SL-75/2 | 15KW | 3.5m³/d | 75*75*1200mm | 1500kg |
SL-90/2 | 15KW | 4m³/d | 90*90*1200mm | 1800kg |
SL-100/2 | 18KW | 5m³/d | 100*100*1200mm | 2000kg |
SL-120 | 15KW | 3.5m³/d | 100*120*1200mm | 1500kg |
SL-145 | 18KW | 3.5m³/d | 145*145*1200mm | 1800kg |
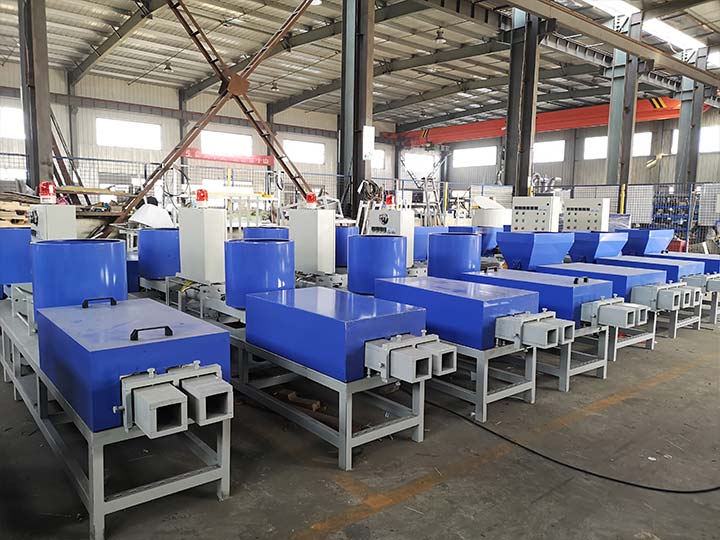
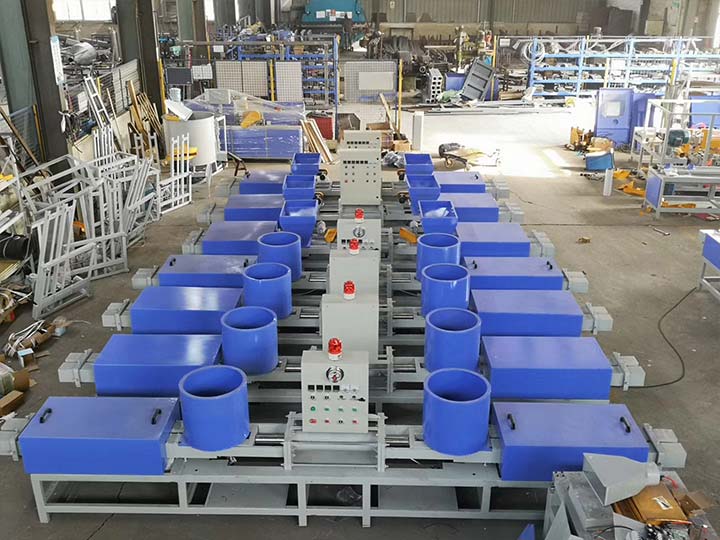
Wood pallet block machine video
Common processing sizes of wood pallet blocks
The length of pallet blocks processed by a commercial wood pallet block machine is usually 1200mm. There are usually many cross-sectional dimensions, mainly determined by different molding dies. Common sizes that can be processed are 75*75mm, 80*80mm, 90*90mm, 90*120mm, 100*100mm, 100*120mm, 100*140mm, 100*150mm, 140*140mm, etc. We can also customize the size of pallet blocks according to customer needs.
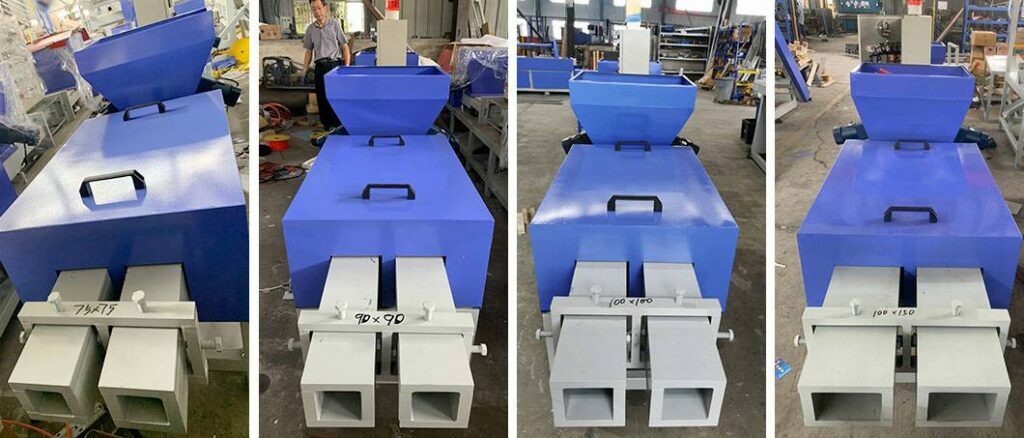
Wood pallet blocks production line
For customers who need a complete set of pallet blocks processing equipment, we can provide a complete sawdust wood pallet blocks production program, namely the wood pallet blocks production line.
Wood pallet blocks processing line is composed of a series of processing equipment, mainly including hammer mill, sawdust dryer, automatic mixer, wood pallet block machine, and pallet blocks cutting machine.
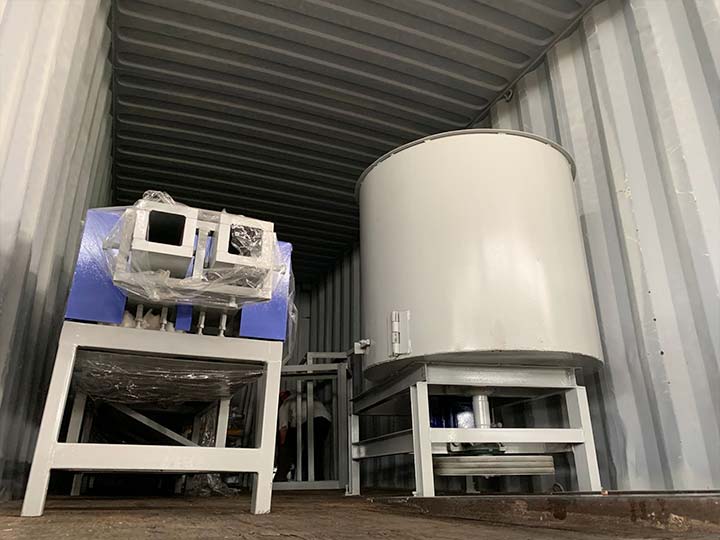
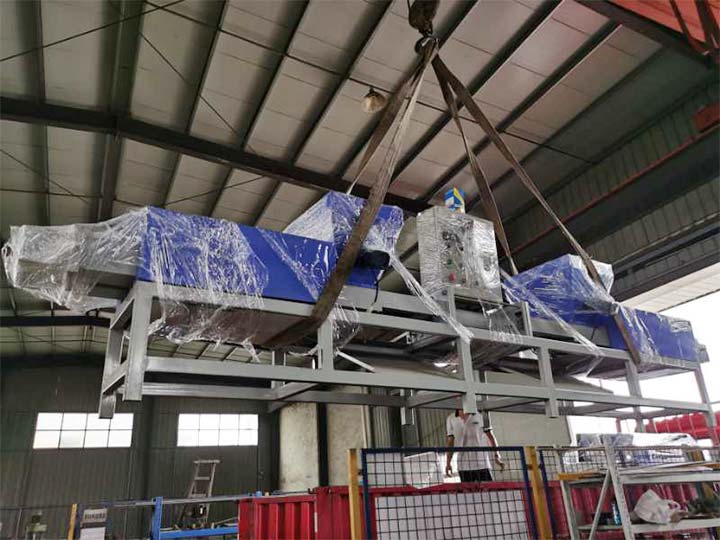

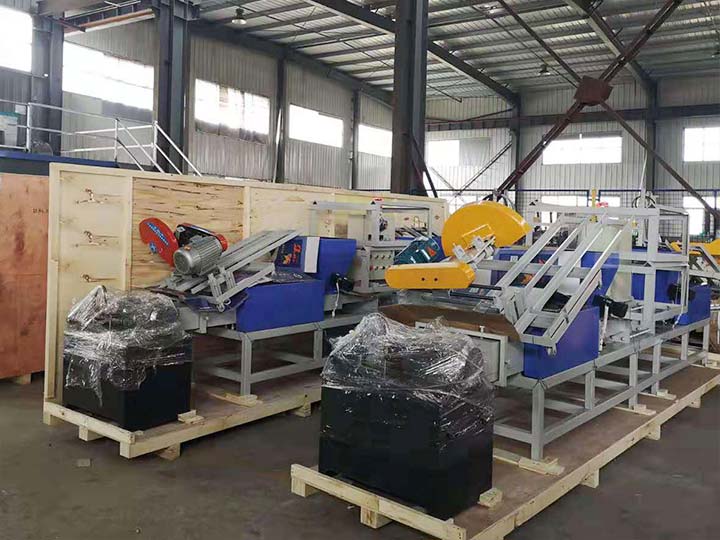
Sawdust pallet block machine shipped to Indonesia
The industrial sawdust pallet block machine can squeeze rice husks, sawdust, and other raw materials into cubes under high temperature and high-pressure conditions. These sawdust pallet blocks can be further processed into wooden pallet feet.
One of our Indonesian customers ordered a complete set of sawdust pallet block machines from our factory, including a glue mixing machine, pallet block press machine, and pallet blocks cutting machine. The Indonesian customer processed sawdust pallet blocks mainly for selling to specializing in the production of wooden pallets factory.
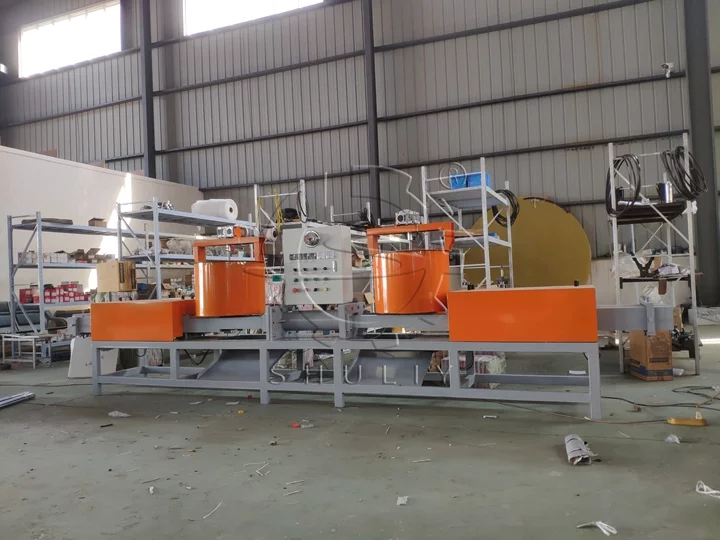
Conclusion
With its efficient heating system, customizable mold options, and continuous extrusion and cutting design, the Sawdust Wood Pallet Block Machine offers a reliable and scalable solution for producing high-strength pallet blocks from various biomass materials.
Whether you are looking to recycle sawdust or enhance your pallet manufacturing line, this machine delivers consistent output and cost-effective performance.
If you’re seeking a durable, fumigation-free alternative to traditional wooden foot blocks, our pallet block machine is the ideal choice to help you meet both domestic and international packaging standards. Contact us today for more details and customized solutions.
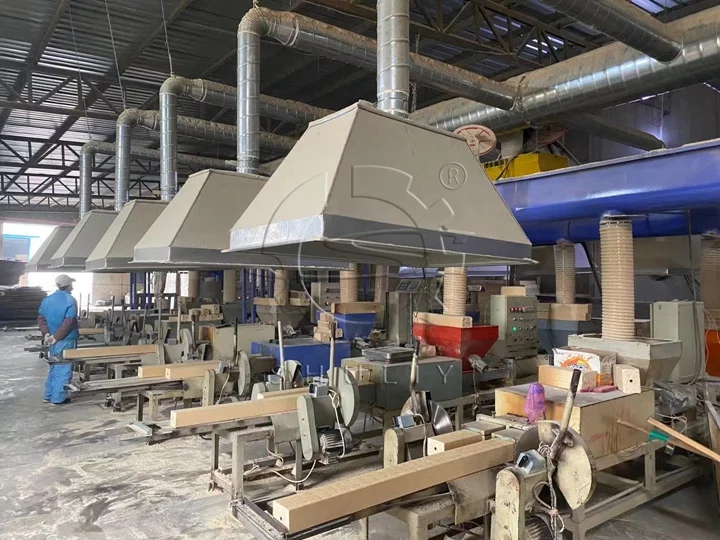